The construction industry has grown significantly in the past few years. And it's providing real returns to building material suppliers, contractors, and others who can capitalize on this boom.
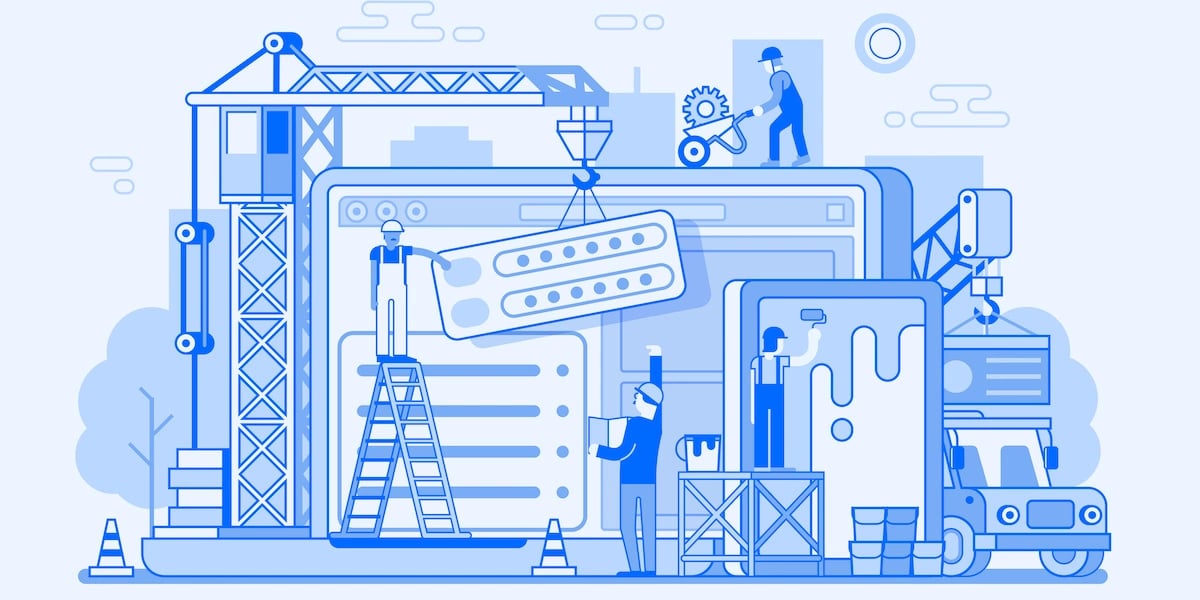
However, suppliers are also facing more challenges than ever when it comes to managing the delivery logistics. These challenges—from over-reliance on manual processes to driver shortages—are weighing heavily on companies’ resources. Fortunately, new technologies can help. They provide construction material manufacturers and suppliers a way to overcome these challenges.
Reducing Last Mile Delivery Costs with a Construction Material Delivery App
A huge number of factors all contributing to increased last mile delivery costs. Luckily, the right construction material delivery app can help. It can give you the tools to boost efficiency and cut costs. Not just that, but the right solution can help delight customers and boost delivery success.
Here's how the right construction material delivery app helps:
Delivery Route Optimization
The distance between two delivery points significantly impacts delivery costs. As such, it’s necessary to optimize multi-stop routes so drivers can make more deliveries per day.
A last mile delivery solution with route optimization features can help you calculate the most efficient routes. How? By considering a number of factors: location, time, distance, driver capacity, traffic, and more.
Crucially, you’ll need to find a solution with routing that’s scalable and efficient. This way, you can route same day delivery requests without your route plans falling apart.
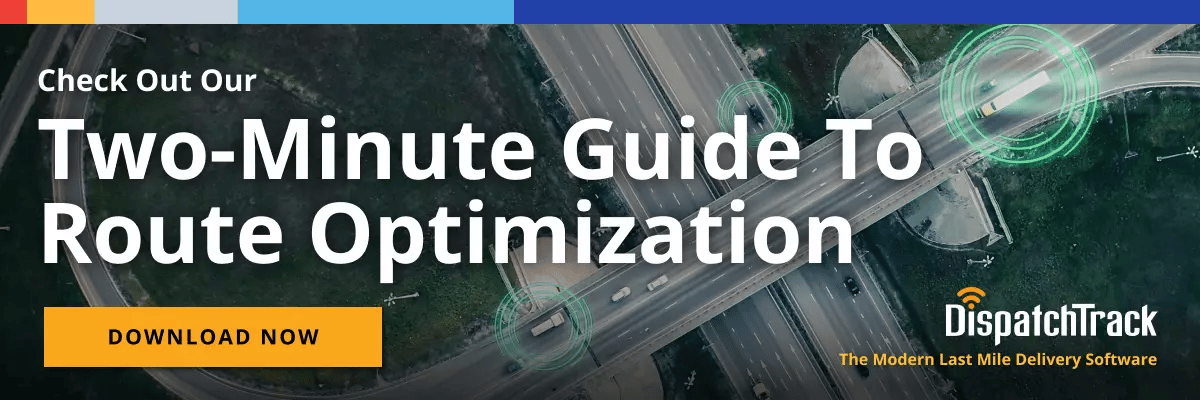
Auto Dispatching
Manual dispatching (i.e. dispatchers handing out printed assignments for the day) is time-consuming and inflexible. But if you can automatically dispatch stops to drivers on the fly with a convenient mobile application, you can actually capitalize on the speed and sophistication of your route optimization.
How? By matching the most suitable driver and truck to the load for delivery. From there, you can send them turn-by-turn directions to the job site.
Real-Time Visibility
Real-time visibility is the ability to monitor and trace orders from pickup at the warehouse to the final delivery. Real-time tracking allows dispatchers and fleet managers to stay on top of each building supplies delivery. You can identify issues drivers may be facing so they can take pre-emptive actions.
This is especially true when it comes to returns, which crop up frequently in construction material delivery. For instance, as a result of over-ordering pipes, insulation, etc.
Electronic Proof of Delivery
The right last mile delivery app helps construction material suppliers capture digital proof of delivery. Ensuring the proper capture and storage of proof of delivery is particularly crucial here. It offers a clear record of the driver who delivered the goods, where and when the goods were dropped off, and who actually signed for them. This is invaluable when the person doing the ordering is different from who’s doing the receiving.
Here, you’ll want a mobile app that enables drivers to collect signatures, notes, and photos within a few seconds. You can then send these to the centralized data hub and access them easily at a later time. Collecting and storing proof of delivery provide fleets with useful insights. They can help fleet managers to verify deliveries, identify challenges, and streamline operations.
Real-Time Reports and Analytics
An advanced construction material delivery app also offers companies crucial real-time insights. You can use these insights to make data-driven business decisions. The right solution provides data such as average time per task, distance covered, idle time, miles per task, number of successful deliveries and tasks completed, number of failed deliveries, and more. This need isn’t specific to construction and building supplies—but it’s still crucially important!
The last mile delivery of construction materials and supplies can be costly and complex. Any construction material supplier needs to stay on top of each delivery to keep delivery costs under control. Fortunately, this is possible with the help of the right last mile delivery app.
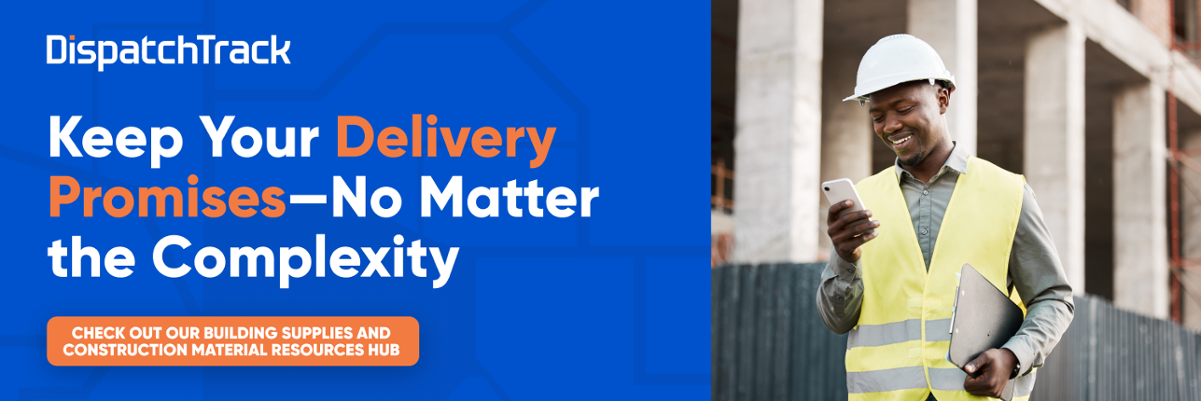