Managing repetitive customer orders, dealing with products with short shelf lives, finding the right trucks and service vehicles for particular order types, keeping track of complex billing requirements—these are just a few of the reasons why food logistics are more difficult to handle than ever. But as last mile technology evolves, some businesses will be able to see their problems and challenges in a new light. Though customer expectations aren’t getting any less stringent, new tools are being introduced every day to help wholesalers, distributors, and others to provide better last mile experiences to their customers.
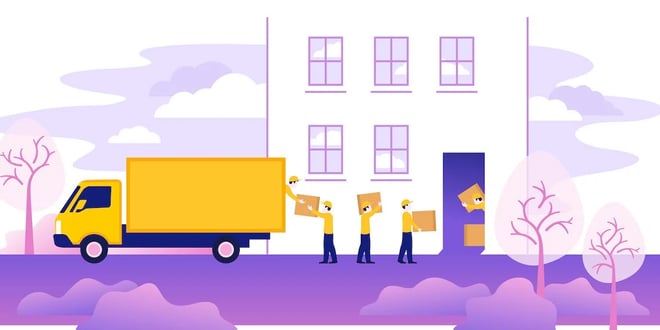
1. Customer Ordering
If your customers are mostly making recurring orders (with some variations), you need to make it as easy as possible for them to indicate their needs and get the items they want.
As such, food distributors must keep information on repeat orders so the ordering process becomes easy. This, in turn, will improve customer relationships, decrease churn, and ultimately increase profitability.
To ensure a painless customer ordering following, food companies need the following:
- The order history of each customer
- The price of each product for each customer and how much they previously paid
- The inventory status of the same products that customers repeatedly order
This brings us to our next challenge….
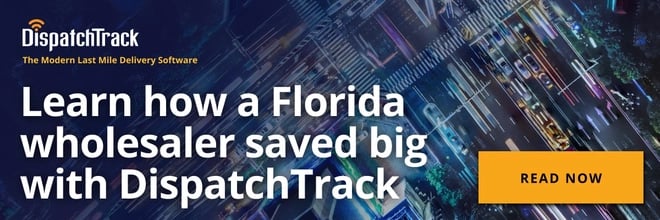
2. Inventory Control
Food companies have to ensure sufficient stock levels to ship at any given time without having any overstock or understock of their inventories. Having adequate supplies at all times requires constant analysis of quantities committed to customer order, inventory level, and volume of product that are expected to be received. Ensuring the right amount of stocks is on hand is crucial in preventing loss of sales due to the lack of inventory or food spoilage because of food expiration.
Improving inventory efficiency is a must. Here are few things to track in order to make that happen:
- Sales trends of the food products
- Real-time inventory levels at all times
- Products' expiration dates
- Delivery dates of products
Generally, this will fall under the heading of warehouse management--but this challenge speaks to a larger hurdle of maintaining visibility across different IT solutions. If you can’t easily sync orders, deliveries, inventory, and other touchpoints, you’re going to run into issues.
3. Efficient Delivery
Consumers these days—especially restaurants, bars, etc.—demand to receive their orders on the promised delivery windows. Businesses are unlikely to gain a strong brand following if they are facing numerous instances of missed orders or partial deliveries.
The food business requires careful organizing, picking, and planning of deliveries—which makes route optimization an absolute must. Enterprises must have access to well-organized and easily available information so they can maximize their on-time delivery rate while getting the most out of their existing delivery capacity.
Excel sheets, duplicate copies, manual processing and route planning: all these should be a thing of the past. Tasks done manually are both error-prone and labor-intensive. The more you can cut them out the delivery process—e.g. by automating your routing and dispatching—the better.
Ideally, you’d be able to automate not just routing, but customer and driver communications as well.
4. Balancing Static and Dynamic Routing
Many of the challenges we’ve discussed above have been fairly typical for last mile delivery—but one of the things that differentiates food logistics is the delicate balancing act that needs to happen between static and dynamic routing.
When you have recurring customers with established delivery windows, you need to be able to rely on pre-established routes without reinventing the wheel every day. At the same time, you need to remain agile, make changes, and accommodate new orders as needed—all of which requires dynamic routing capabilities.
In short, the only path forward for optimizing the last mile in food logistics is a hybrid routing model that combines the two. This, of course, should exist within the kind of routing functionality we’ve been discussing above. At a high level, you should be able to:
- Automate route planning, eliminating the time-consuming job of manually plotting routes. Drivers will then receive their assignments, delivery sequence, and route plans automatically, reducing their wait times at the warehouse.
- Perform route recalculation or rerouting should drivers encounter unexpected events like road closure, a sudden downpour, accidents, or sudden heavy traffic
- Provide drivers with needed information about each drop-off point
- Generate dispatch reports that provides the wait times at each drop-off point as well as other special instructions during deliveries
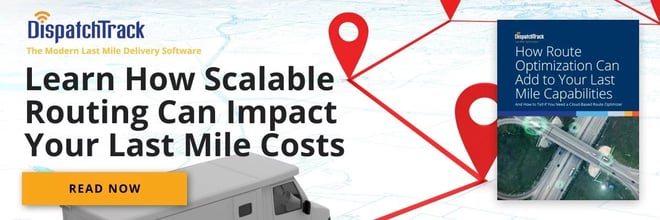
5. Food Recalls
Last but certainly not least: Food products are susceptible to recalls. Thus, it's essential for the business to have the ability to track their products via a master list that has all the important information, such as manufacturing date and delivery recipients among others. Tracking products is the responsibility of all food manufacturers and distributors. Tracking allows them to remove products that have been tagged as unsafe as effectively and quickly as possible.
Failing to track products and remove them from the market as necessary will put the public at risk. Food manufacturers and distributors should keep in mind that time is of the essence when it comes to product recalls. Small to medium-sized food companies might face serious legal and economic consequences when food recalls happen. Ensuring effective product traceability requires the following:
- Recording of product lot numbers every time products are received into the warehouse
- Maintaining the traceability of raw materials as applicable
- Managing the movement of each and every product effectively especially during delivery—if there’s something unexpected left over in the truck after the last run, you need to be able to figure out what happened
- Identifying the location of every product lot quickly
Supply chain and logistical processes are complex enough to begin with—often more so for food companies. Food is perishable and businesses are likely to suffer major financial losses when they get damaged or spoiled, or if there’s a failure in tracing the products during recalls. Overcoming these challenges in food logistics, however, is possible with the right technology.